Z3
Simply Amazing
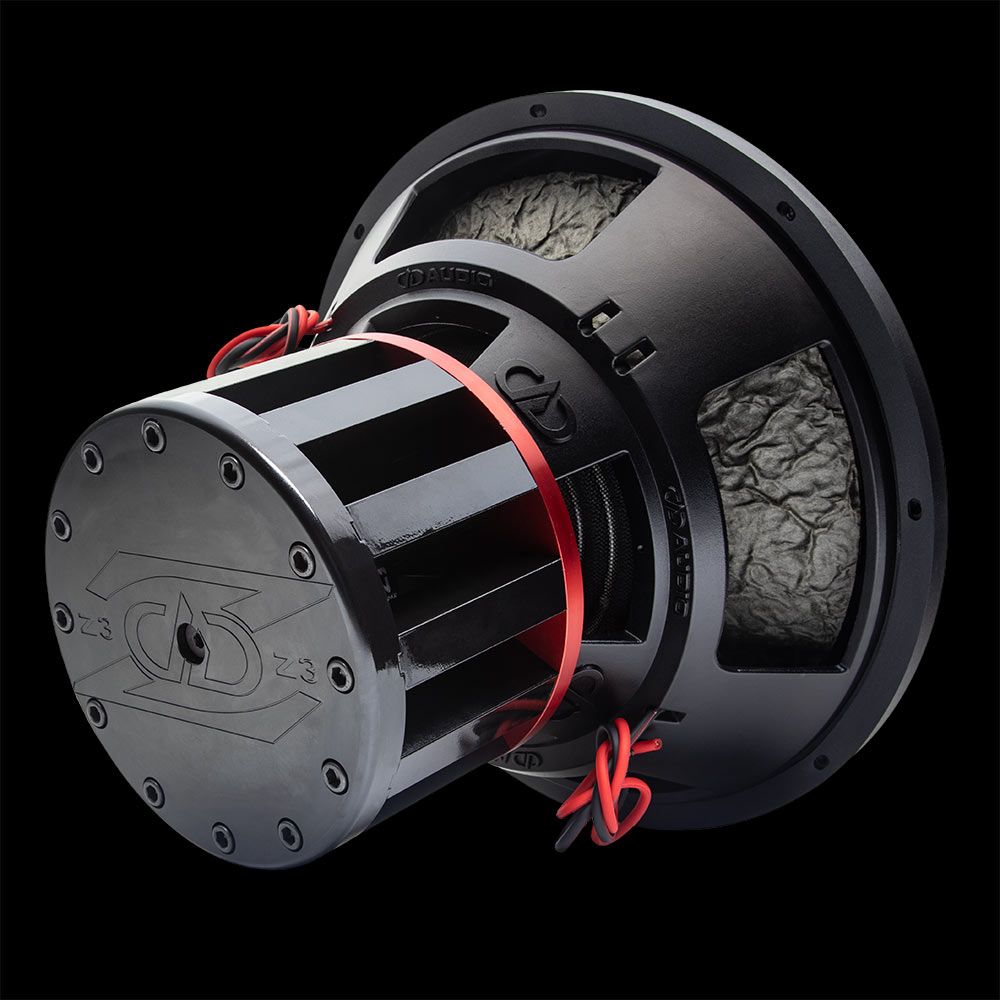
Search Authorized DD AUDIO Dealers Near You
CarMedia PRO s.r.o.
Obránců Míru 487, 50302 Předměřice nad Labem, CZECH REPUBLIC
David’s Street Sound Automobile Entertainment
271 Dr. Sixto Antonio Avenue, Pasig, Metro Manila, Philippines
HI-FI CAR CENTER
Corso Pietro Pisani, 164, Palermo, Province of Palermo, Italy
Z-Past
In early 2005 the first-ever iteration of the Z motor was launched. It forever changed the way people thought of a high-performance subwoofer and pushed the limits of car audio to new extremes. Over the years, many versions of Zs have been produced and this spirit of experimentation has driven us to constantly improve and innovate... This sub rightfully takes its place as one of the most dominant competition subs of all time even though it wasn’t actually designed for competition. The motivation behind the Z was simply to build the best sounding high power handling driver of all time; to that note DD Audio considers the Z mission accomplished.
Z-Present
All the moving parts are USA made from the finest materials and manufacturing methods available. All parts are then assembled and QC’ed in our OKC facility. The current generation Z3 is a grade 52 neodymium open motor design. The bottom of the motors are engraved with the DD Z logo and series. All steel motor parts use black painted gloss finish that provides excellent corrosion and heat resistance, while minimizing coating thickness and maximizing energy transfer between motor parts. To further compliment the Z’s striking motor cosmetics the aluminum quick-change top plate, and shorting ring both feature red anodized accents. You’ll notice the standard TS parameters are missing for the Z subs. This omission is on purpose because each Z is custom built to order allowing for Zillions of possible parameter sets making one static set of specs very prone to inaccuracy. The reason we build Zs custom to order is it gives a system designer the utmost freedom to design for their specific application. The Z Series subs also feature our Evolution Subwoofer Package (ESP). ESP equipped drivers sport larger diameter suspensions and deeper frames than standard subs and exclusive surround and cone designs. ESP subs are truly built to maximize performance in their designated size class. The Z Series comes standard with an oversized dry finish black composite dust cap, red logo, and treated pulp cone, but it can be optioned out with custom suspension configurations, alternative composite dust caps, composite cones, powder-coated frames, and a multitude of logo options to give your sub a personalized look and/or added performance for a specific application.
Z-Future
DD Audio will continue down the path of global transducer domination via the sledgehammer of the subwoofer world…
THE Z
Each run of DD AUDIO Z Subwoofer is unique and subject to cosmetic differences from the image shown.
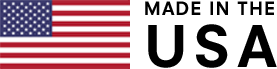
CUSTOMIZE YOUR SUB

Express yourself with your choice of logo style and color, plus custom dust cap and cone!
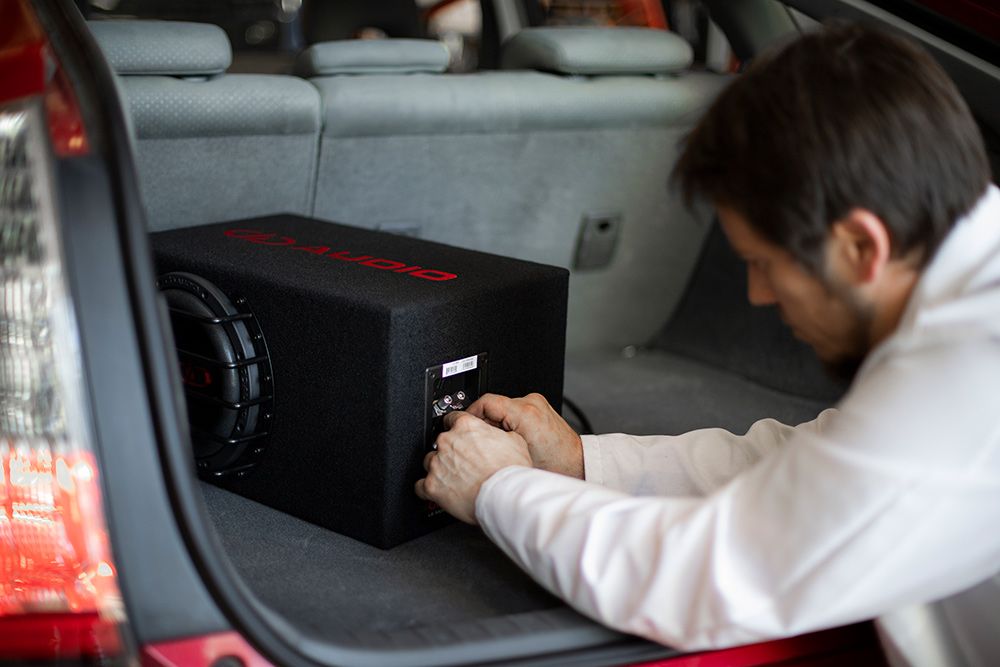
Support Small Business and Enjoy Expert Installation
We believe in supporting brick and mortar dealers and have carefully partnered with small businesses who can provide quality installation and customer satisfaction befitting DD AUDIO® equipment.
Check with your local dealer for stock and promotional discounts.